Selective plasma oxidation of FeCrAl alloys for extended-lifetime of glow plugs for diesel engines (L2-8181)
Project leader: Prof. Dr Janez Kovač (Jozef Stefan Institute)
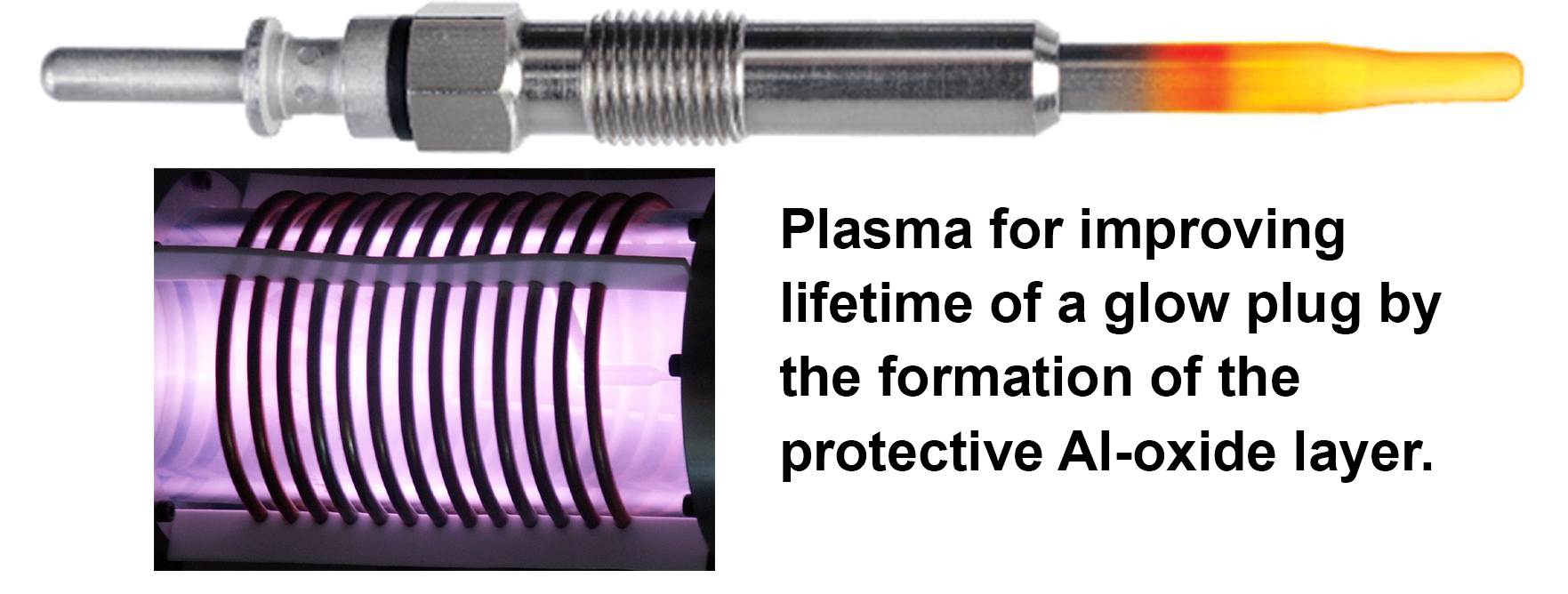
The service life of a glow plug in a diesel engine is limited by the lifetime of its heating resistor which is usually made in the form of a wire from the high-temperature-resistive alloy Fe-Cr-Al and operates at 1200 °C. A protective oxide scale of -Al2O3 is formed on the surface of the wire, which protects it against the diffusion of foreign atoms from and to the surrounding atmosphere. However, mechanical stress, thermal shock, different temperature-expansion coefficients of the oxide scale and the substrate may lead to spallation of the Al2O3 protective scale and to degradation of the resistor and, finally, to the failure of the glow plug. There are a variety of approaches used to avoid such damage to the protective oxide scale, but they do not resolve this problem.
Our proposal to avoid failure of the Al-oxide film at high temperature and thereby extend the lifetime of the glow plug is the formation of a nanocomposite and homogeneous Al-oxide protective scale/film on the Fe-Cr-Al alloy by selective low pressure plasma oxidation and by the use of modified Fe-Cr-Al alloys. To the best of our knowledge, such a solution has not been proposed before. An oxide film prepared by plasma oxidation should have much better adhesion. Our group at the Jozef Stefan Institute has many years of experience in this field. We propose a low pressure plasma treatment as a proper combination of a reductive and an oxidative plasma treatment using H2 and O2 gases in a two-stage process to provide the selective and controlled formation of a compact and homogeneous Al2O3 layer on the Fe-Cr-Al alloy. The thickness of such a film can be tuned in the range 20–500 nm. Preliminary trials performed on heating wires that were selectively oxidized using a low-pressure plasma in our laboratories and tested at our industrial partner in this project (Hidria AET) show very promising results. In the project we will study the two-phase plasma treatments investigating the duration of phases, the oxidation rate as a function of the density of ions and the neutral species in the plasma, the degree of dissociation, the type of plasma and the discharge conditions. Life-time measurements of the modified glow plugs will be performed at the industrial partner Hidria AET. The third partner in the project (NTF Uni-Lj) will prepare alloys with an increased concentration of Al and other reactive metals (Ti, Zr) by melt-spinning. In this way the influence of alloying elements on the kinetics of oxidation will be followed. Due to changes in the surface chemistry introduced by the plasma oxidation of the heating wires it will be necessary to adopt the existing joining technology for the oxidized heating element on the tube of the glow plug. This will be performed by the fourth project partner (Faculty of Mechanical Engineering, Uni-Lj).
We plan to protect the innovative technology derived from the project with international patents, after which we plan to publish the main results in scientific journals. We expect that the improved performance of the glow plug will extend its lifetime by 10-20 %. In this way the industrial partner will gain an advantage over the competition, increase its market share and added value for this product. New generation of glow plugs will fulfil ecological standards, like EURO VI and EURO VII, which are related to lower emissions of nitrogen oxides (NOx) and solid particles having a positive impact on health and general living conditions. The number of employees at Hidria AET is also expected to increase due to the production process of the new product.